Unique Combination Clutch-Slip Device from Reell Powers and Protects Bosch Pro Hedge Trimmer
When Bosch created a new line of professional hedge trimmers for the vast hedgerows that populate the UK and European countryside, it needed a tool that was both powerful and safe. One of the early design challenges the company faced was providing a clutch mechanism that would disengage the oscillating blade if the operator took his hands off the grips. When engaged, the clutch had to be able to supply the torque needed to cut through the occasional thick branch without slipping. At the same time, the mechanism had to protect the drive gears from damage if the trimmer encountered something tougher – like a chain link fence. And, it had to be durable, lightweight and compact.
To help meet this complex series of performance characteristics, Bosch turned to Reell Precision Manufacturing in St. Paul, MN for its expertise in small-package torque control. Working through Reell’s European facility in the Netherlands, Reell was able to design and manufacture a compact mechanical clutch based on its wrap spring clutch technology. Also built into the mechanism was a constant-torque slip device based on the company’s patented clip and shaft technology. One technology provided a way to disengage the cutting blade from the motor to improve safety for the operator – the other sets an upper torque limit to protect the motor gears in the event of striking an obstacle.
Powerful tool required protection
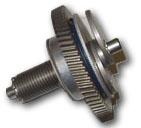
“This particular hedge trimmer is designed for professional landscapers, and is a very powerful tool that generates more than three-quarters of a horsepower,” says John Kossett, a Reell project engineer in St. Paul who led the development of the clutch design. “The motor constantly spins at about 25,000 rpm and is geared down to turn the clutch at just 1,500rpm. Acting like an on-off switch, the clutch engages the blades when the operator grips the handles with both hands. If the trimmer hits something it can’t cut through, the blades will stall instantly. However, since the armature of the motor is spinning at 25,000 RPM, it has a lot of kinetic energy in the form of momentum. If there is no ‘give’ anywhere in the system, the small drive gear tends to fail. The built-in slip device allows the kinetic energy to be dissipated over about a half revolution of the clutch, safely slowing and stalling the motor.”
The design of the combination clutch-slip device represented something of a technological breakthrough for both Reell and Bosch. Bosch was able to create a safe and ergonomic trimmer that delivers high power in a very compact, lightweight trimmer. And, for Reell, it represented the first time a wrap spring clutch of theirs was used to control a new high of 80 Newton-meters (708 lb-in) of torque in such a small device. Reell’s design of the integral slip device was derived from the technology used in its line of constant-torque hinges, and this was the first time its clip technology was implemented in such a high torque range, according to Kossett.
Operator safety was improved
“The new patent-pending clutch-slip device design has also improved safety,” says Kossett. “In their previous design, the motor took 1.5 seconds to stop after the operator took a hand off the interlock device in the trimmer’s grip. Now, with the Reell clutch, the blades stop in less than 0.1 seconds, greatly reducing the possibility of operator contact with the moving cutters.” This improved performance is based on the characteristics of the wrap spring clutch, which can engage and disengage quickly and consistently even under heavy load.
In a wrap spring clutch, a coil spring rotates with the drive motor. The output shaft, or driven part, is located down the center of the spring’s coil. If the tail of the spring is moved opposite to the direction of its windings, the coil expands and disengages the output shaft. If the tail of the spring is allowed to relax, the coil shrinks and grabs the shaft, transferring the rotation to the output. Known for their relatively high torque for a given size and consistent engagement timing, wrap spring clutches have found wide application where there is a need to control rotary motion.
Reell had design and manufacturing capability
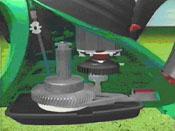
After Reell designed the clutch-slip device, Bosch was interested in having Reell manufacture the devices as well. Bosch wanted a European-based
manufacturer to produce the clutch assembly so it could be transported quickly and cost-effectively to Bosch’s production facility in Switzerland. The two companies worked together to develop a state-of-the-art production line at Reell’s factory in the Netherlands. The new production line is not only semi-automated, it performs 100 percent functional testing of each completed assembly. The testing assures consistency between parts, and also detects and sets aside non-conforming products, avoiding the potential costs of sorting or rework at the customer’s location.
According to Peter Heywood, Bosch Project Manager, “Reell’s engineers quickly took up the challenge and delivered on the most difficult requests. This was truly an international project that included Bosch’s UK-based engineering team, Reell’s US-based design team, Reell’s production facility in the Netherlands, and final assembly at Bosch’s facility in Switzerland.”